In the realm of material science and industrial quality control, hardness testing stands as a critical pillar for assessing the durability, strength, and reliability of materials. From manufacturing to construction, aerospace to automotive industries, the ability to accurately measure hardness ensures the integrity and safety of various components and structures. The Brinell hardness test is a widely used method that determines the hardness of a material by measuring the diameter of an indentation caused by a standardized load. While traditional brinell testers have served well over the years, the advent of digital technology has ushered in a new era of precision and efficiency. This article explores the innovative advancements of digital brinell hardness testers.
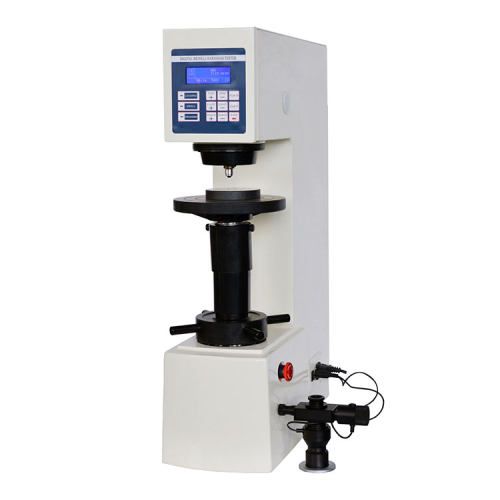
Traditional Brinell Hardness Testing Method
The Traditional Brinell Hardness Testing Method is a technique used to measure the hardness of materials, particularly metals. It was developed by Swedish engineer Johan August Brinell in 1900. The Brinell hardness test is based on the principle of identifying the impression made by a hardened steel ball into the surface of the material being tested.
Pros and Cons of Traditional Methods
The Traditional Brinell Hardness Testing Method offers several advantages and disadvantages:
Pros:
- Simple Procedure: The Brinell test is relatively straightforward and easy to perform compared to some other hardness testing methods.
- Large Indentation Size: The large size of the indentation allows for reliable hardness measurements, especially for materials with coarse grain structures or heterogeneous compositions.
- Wide Range of Materials: The Brinell test can be applied to a wide range of materials, including metals, alloys, and even some non-metallic materials.
- Accuracy: When performed correctly, the Brinell test provides accurate hardness measurements that are useful for material characterization and quality control.
- Repeatability: The test can be repeated multiple times with consistent results, allowing for reliable comparisons between different samples.
Cons:
- Surface Preparation Requirement: The surface of the material being tested must be flat, smooth, and free from contaminants, which may require time-consuming preparation.
- Limited Application for Thin Materials: The Brinell test is not suitable for very thin materials or parts with limited space for indentation.
- Large Equipment Size: The testing equipment used for Brinell testing, including the testing machine and microscope, can be large and bulky, making it less suitable for field testing or on-site applications.
- Indentation Visibility: In some cases, especially for harder materials, the indentation may be difficult to measure accurately, leading to potential errors in the hardness reading.
- Long Test Duration: The Brinell test typically requires a longer duration compared to other hardness testing methods, which may not be suitable for high-volume production environments.
In summary, while the Traditional Brinell Hardness Testing Method offers several advantages such as simplicity, accuracy, and suitability for a wide range of materials, it also has limitations related to surface preparation requirements, equipment size, and applicability to thin materials. Understanding these pros and cons helps in determining the most appropriate hardness testing method for a given application.
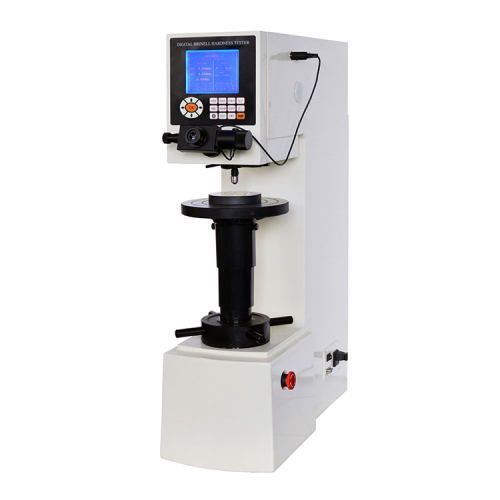
Emergence of Digital Brinell Hardness Testers
Digital Brinell hardness testers are advanced machines that measure the hardness of materials. They do this by applying a force to a material with a hardened steel ball indenter. The diameter of the indentation left on the material is then measured, and this is used to calculate the Brinell hardness number (HB).
Features of Digital Brinell Hardness Testers
Here are some of the features and functionalities of digital Brinell hardness testers:
Automatic measurement cycle: This feature allows the tester to automatically apply the test force, dwell at the peak load for a set time, and then unload the indenter. This eliminates the possibility of operator error and ensures that all tests are performed consistently.
Large, easy-to-read digital display: This feature makes it easy to read the test results, even in poorly lit conditions.
Multiple test scales (HBW, HBS, HV): Some digital Brinell hardness testers can also measure the hardness of materials in other scales, such as Rockwell and Vickers. This can be useful if you need to compare the hardness of a material to a specification that is given in a different scale.
Data storage and retrieval capabilities: Many digital Brinell hardness testers can store the results of tests in memory. This data can then be retrieved later for analysis or reporting.
Statistical analysis of results: Some digital Brinell hardness testers can perform statistical analysis of test results, such as calculating the average, standard deviation, and coefficient of variation. This can be useful for quality control purposes.
User-friendly interface: Digital Brinell hardness testers typically have a user-friendly interface that makes them easy to operate. This can be important for users who are not familiar with hardness testing.
Closed-loop control for precise test results: Closed-loop control ensures that the test force is applied accurately and consistently. This helps to ensure the accuracy of the test results.
Automatic test head positioning: Some digital Brinell hardness testers have automatic test head positioning. This can help to save time and improve the accuracy of tests.
Capability to test on a variety of materials: Digital Brinell hardness testers can be used to test a wide variety of materials, including metals, plastics, and ceramics.
Overall, digital Brinell hardness testers are versatile and easy-to-use machines that can provide accurate and reliable measurements of the hardness of materials.
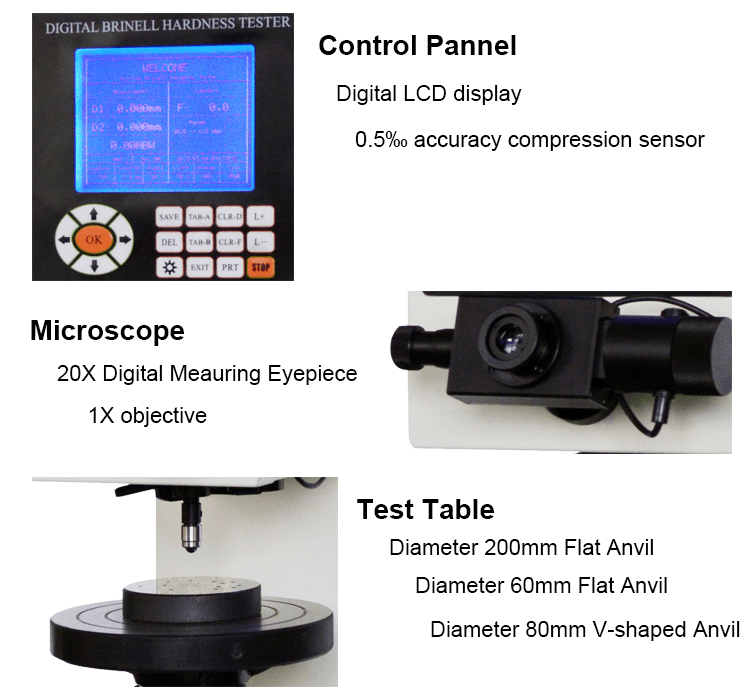
Comparison between Traditional and Digital Brinell Hardness Testers
The transition from traditional to digital Brinell hardness testing brings several advantages. Digital testers offer faster testing times, increased accuracy, and the ability to capture and store data digitally. The automated nature of digital testers also reduces the dependency on skilled operators, making hardness testing more accessible to a broader range of users.
While traditional methods have their merits, the benefits offered by digital Brinell hardness testers are increasingly making them the preferred choice in modern materials testing laboratories. Here are the comparisons:
Feature | Traditional Brinell Hardness Tester | Digital Brinell Hardness Tester |
Measurement | Manual, using a microscope | Automatic, electronic measurement |
Accuracy | Prone to operator error | High accuracy due to closed-loop control |
Efficiency | Time-consuming | Faster testing due to automation |
Data storage | Limited | Electronic data storage and retrieval |
User-friendliness | Requires operator skill | User-friendly interface |
Applications of Digital Brinell Hardness Testers
Digital Brinell hardness testers are widely used in various industries for assessing the hardness of metallic materials. Some of the key applications include:
Quality Control in Manufacturing: Digital Brinell hardness testers are used in manufacturing industries to ensure the quality and consistency of materials. By measuring the hardness of metallic components, manufacturers can verify that the materials meet specified standards and requirements.
Material Selection: Engineers and material scientists use Brinell hardness testing to select appropriate materials for specific applications. By determining the hardness of different materials, they can assess their suitability for various industrial purposes, such as automotive components, construction materials, and tooling.
Research and Development: In research and development laboratories, digital Brinell hardness testers are used to study the properties of different materials and evaluate their performance under various conditions. Researchers can use hardness data to optimize material formulations and manufacturing processes.
Failure Analysis: When components fail in service, hardness testing can help determine the cause of failure. By examining the hardness profile of a failed component, engineers can identify areas of excessive stress, material defects, or other issues that may have contributed to the failure.
Welding and Heat Treatment: Digital Brinell hardness testers are used to evaluate the effectiveness of welding and heat treatment processes. Hardness measurements can help ensure that welds have sufficient strength and that heat-treated materials have the desired mechanical properties.
Quality Assurance in Construction: In the construction industry, Brinell hardness testing is used to assess the hardness of structural materials such as steel and concrete. By ensuring that construction materials meet specified hardness requirements, engineers can guarantee the integrity and safety of buildings and infrastructure projects.
Automotive and Aerospace Industries: In automotive and aerospace applications, Brinell hardness testing is used to evaluate the hardness of engine components, structural parts, and other critical elements. Hardness data is essential for ensuring the reliability and performance of vehicles and aircraft.
Overall, digital Brinell hardness testers play a crucial role in ensuring the quality, reliability, and safety of materials and components across various industries.
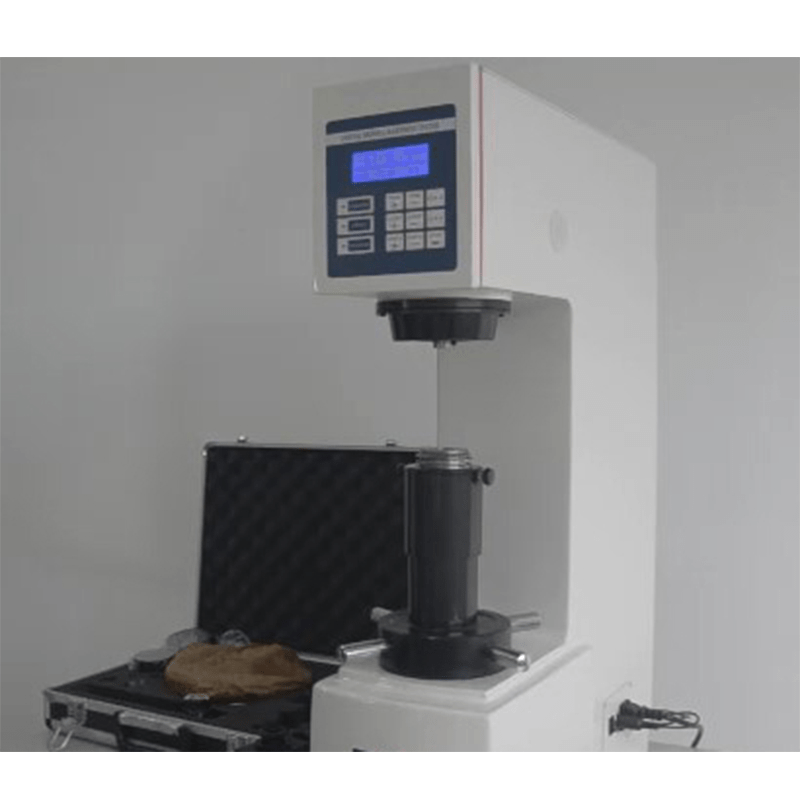
Conclusion
The introduction of Digital Brinell Hardness Testers marks a significant milestone in the evolution of materials testing. These innovative devices not only streamline the testing process but also elevate the accuracy and efficiency of hardness assessments. As industries continue to embrace digital technologies, the role of Brinell hardness tester suppliers becomes increasingly vital in providing businesses with the tools they need to stay at the forefront of material science and quality control. The transition from traditional to digital Brinell hardness testing signifies a positive shift towards more advanced and reliable testing methodologies in the ever-evolving field of materials engineering.