The process of getting ready for the microscopic inspection of metallographic samples involves grinding and polishing them. To create a perfect, flat surface free of flaws, the material must be removed from the surface of the sample. A range of abrasive materials, from coarse to fine, are used for this. Grinding and polishing metallographic samples is crucial because it enables metallurgists to closely inspect the microstructure of materials. The purpose of this article is to give readers the information and abilities needed to operate a metallographic sample grinding and polishing machine effectively.
3 Tips for Choosing a Metallographic Sample Grinding and Polishing Machine
- Consider the types of samples that you will be preparing.
Various sample types require distinct ways of preparation. For example, a distinct grinding and polishing procedure is needed for soft materials like copper and aluminum compared to hard materials like steel and tungsten carbide. Furthermore, certain materials might be more vulnerable to particular kinds of harm when they are being ground and polished. For example, extreme heat can distort some metals, while ceramics are prone to cracking. Selecting a machine with the features and capacity to prepare your samples without causing damage is crucial.
- Think about the desired surface finish.
Surface finish requirements vary depending on the application. For example, you will require a highly smooth surface finish if you are looking at a material’s microstructure to find flaws. However, a less smooth surface finish could be acceptable for assessing a material’s grain size. The selection of polishing wheels and abrasives will also depend on the required level of surface finish. For example, you might need to use a succession of extremely fine abrasives and polishing wheels to get a very smooth surface finish. You might be able to get away with using a single polishing wheel and a coarser abrasive if a less polished surface finish is acceptable.
- Choose a machine with the appropriate features and capabilities.
Various machines have varying capacities. Certain machines are more feature-rich than others, and some offer a greater variety of speeds—for example, automatic sample loading and unloading. Selecting a machine with the features and capabilities required to accurately and effectively prepare your samples is crucial. There are also some differences among the kinds of Cqscope’s metallographic sample grinding and polishing machine. For example, the YMPZ-1 automatic metallographic sample grinding and polishing machine is a single-disc operation, and the YMPZ-2 automatic metallographic sample grinding and polishing machine is a double-disc operation.
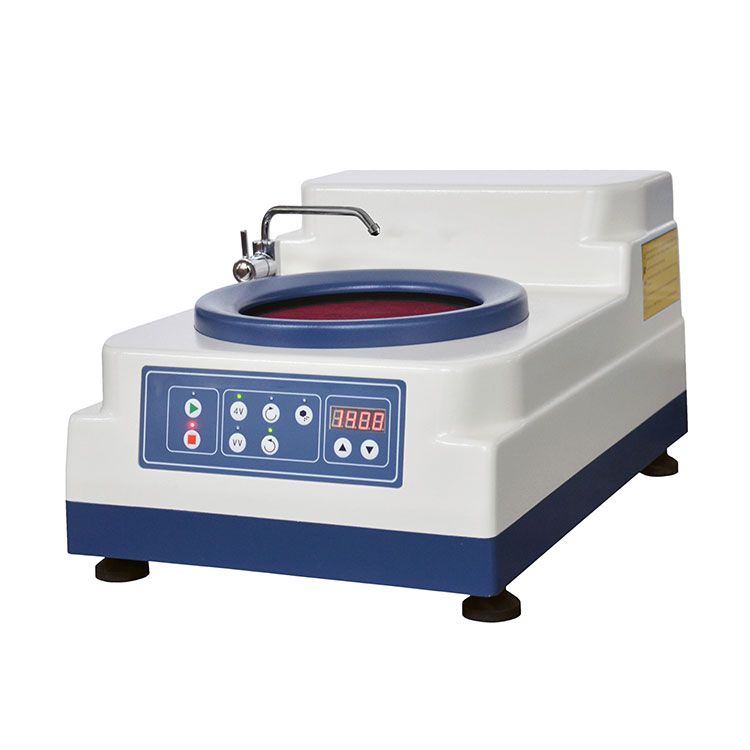
5 Tips for Using a Metallographic Sample Grinding and Polishing Machine
- Prepare the sample properly.
It may significantly affect how well the final surface finish turns out. A well-prepared sample will be less likely to be harmed during the grinding and polishing process and will be easier to work with.
- Use the correct abrasive for each grinding and polishing step.
The cutting capabilities of various abrasives vary. A flawless surface finish is achieved using fine abrasives, whereas coarse abrasives are utilized to remove a lot of material quickly. Use the incorrect abrasive for a given phase to avoid damaging the sample or not removing enough material. You can’t get a smooth surface finish, for instance, if you use a coarse abrasive for the last polishing stage.
- Apply the correct pressure and speed.
An excessive amount of pressure can cause the sample to overheat or distort its microstructure. Applying insufficient pressure will result in insufficient material removal or an uneven surface finish. Overdoing the grinding or polishing process might cause the sample to overheat and even harm its microstructure. It will take longer to prepare the sample and you might not be able to get a good surface finish if you grind or polish it too slowly. Depending on the kind of sample, the abrasive being used, and the required surface polish, different pressure and speed combinations will work. To determine the ideal parameters for your specific sample preparation procedure, it is crucial to conduct experiments.
- Cool the sample adequately.
It can stop the sample from getting too hot. The sample may sustain damage from overheating if its microstructure is distorted and surface oxidation results.
- Clean the sample thoroughly between steps.
It keeps the polishing and grinding wheels and samples from becoming contaminated.
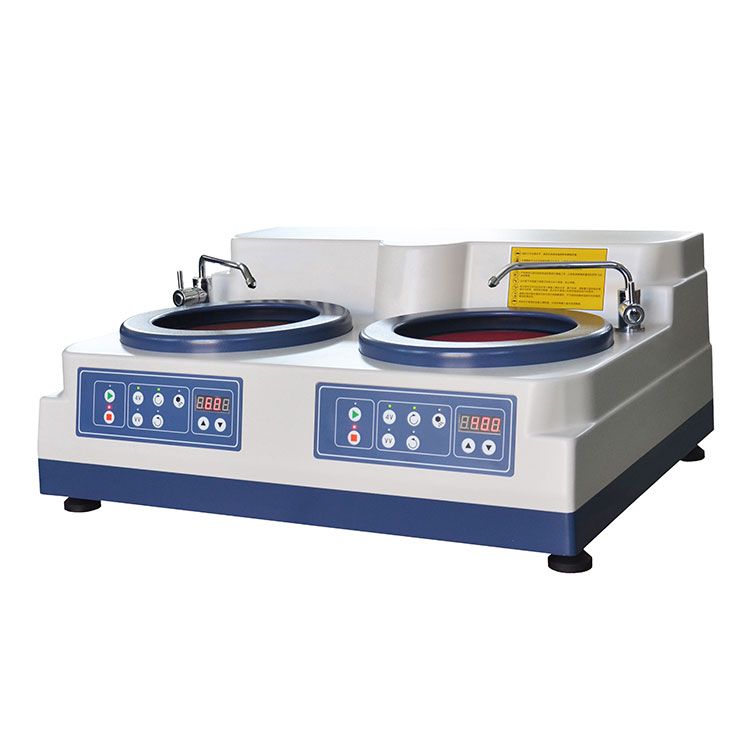
4 Tips for Maintaining a Metallographic Sample Grinding and Polishing Machine
- Keep the machine clean.
It keeps grime and other impurities from accumulating. These impurities have the potential to harm the samples being processed as well as interfere with the machine’s ability to function.
- Lubricate the moving parts regularly.
It lessens wear and friction on the moving parts. The parts may overheat and quickly wear down as a result of friction. By lowering heat and friction, lubrication helps to prolong the life of the parts and enhances machine performance. Among the many moving parts of metallographic sample grinding and polishing equipment are spindles, gears, and bearings. Regular lubrication is necessary to keep these elements functioning smoothly and effectively. Your particular machine will determine the kind of lubrication you need to use. It’s crucial to refer to the manufacturer’s instructions to find out the appropriate kind and quantity of lubrication to use.
- Check the abrasives for wear and tear.
It guarantees that the abrasives are still working and aren’t causing any harm to the samples that are being prepared. When polishing and grinding a sample, the material is removed from its surface using abrasives. The abrasives will deteriorate and lose their effectiveness with time. The samples being prepared may begin to suffer harm if the worn-out abrasives are not changed.
- Replace the abrasives when necessary.
It guarantees that the equipment is working well and that the samples being prepared are not being harmed. When polishing and grinding a sample, the material is removed from its surface using abrasives. The abrasives will deteriorate and lose their effectiveness with time. The samples being prepared may begin to suffer harm if the old abrasives are not changed.
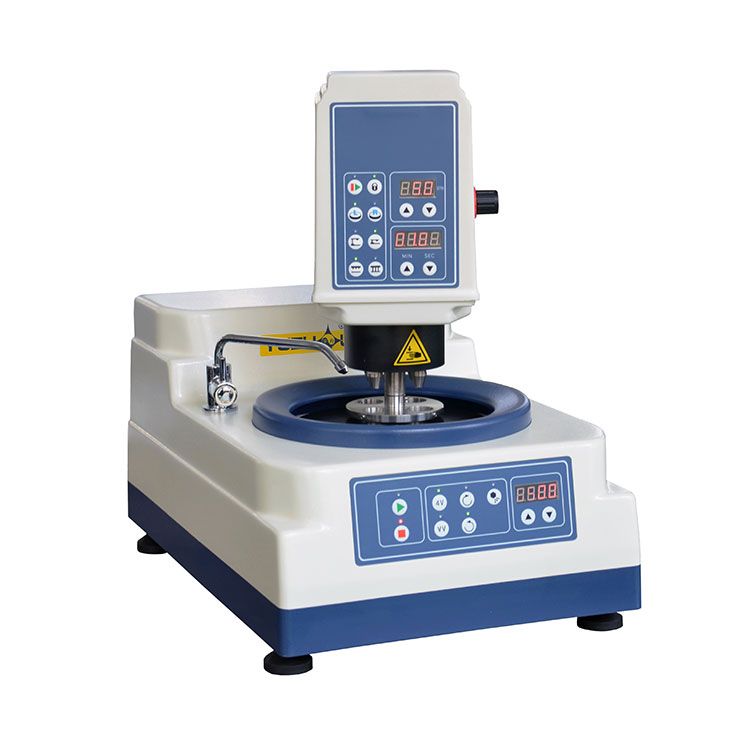
Conclusion
The microstructure of materials is examined using metallographic samples, which is crucial for comprehending their characteristics and functionality. You can create high-quality samples with a smooth surface finish and no defects by utilizing a metallographic sample grinding and polishing machine according to recommended practices. This will enable you to get precise and trustworthy information regarding the material’s microstructure. Machines for polishing and grinding metallographic samples are costly pieces of machinery. You can prolong the machine’s lifespan and lessen component wear and tear by utilizing it according to recommended guidelines. You will save money on time and replacement costs by doing this.